- The next website linking is only available in Chinese.
- If you have any questions, please dial +886-2-2311-2031.
Continue to the website.
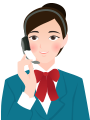
2023-09-28
Carbon emissions are mostly generated during the “driving stage” of the life cycle assessment (LCA) of vehicles. As such, the primary trend is reducing fuel consumption and transitioning towards electric or hydrogen energy. Therefore, this article will explore the 4 major strategies of major global manufacturers: electrification technology, adopting eco-friendly materials, energy transitioning for manufacturing faciities, and circular recycling.
The top global automakers are actively expanding their lineup of electric vehicles. Amongst European automakers, the EU has pledged to achieve carbon neutrality by 2050 and ban sales of fuel vehicles in 2035. German automakers such as VW, Audi, BMW, and Mercedes-Benz have all responded positively to this policy.
LCA reveals that batteries are the key to decreasing the carbon emissions of a whole vehicle. The source of electricity for charging batteries, as well as the manufacturing technology, will affect the overall emissions of the vehicle throughout LCA.
Within the automotive sector, numerous automakers are proactively advancing the research and implementation of fuel cell systems for/towards decarbonization and bolstering energy security, as exemplified in the following cases:
Steel production, a major part of vehicle manufacturing, is one of the main sources of carbon dioxide emissions. All major global steel companies are actively seeking solutions to this problem. By substituting with hydrogen, there is a global effort to achieve an eco-friendly steel production process. The following are some examples:
However, the promotion of green steel is currently facing three major challenges. The industry needs a sufficient supply of renewable energy and green hydrogen, as well as enough waste steel. The third challenge is that current technologies still need to catch up, such as direct reduction hydrogen - electric furnace technology. The industry and governments need to work together to promote production and application of eco-friendly steel.
Although the initial expenses of adopting advanced manufacturing equipment in factories can be substantial, these investments have resulted in substantial energy savings as the car manufacturing industry undergoes its digital transformation.
For example, Japanese company Omron provides smart factory diagnosis services to visualize data like carbon dioxide emissions, electricity, energy consumption, and output. On the other hand, major German automakers use renewable energy to meet energy saving targets. VW factories are generating their own solar energy, while Mercedes-Benz has partnered with German energy suppliers to purchase solar, wind, and hydro energy.
Casting and aluminum alloy die-casting generate the highest amount of carbon emissions in the manufacturing process due to the substantial heat energy required. In casting, energy consumption rises during material heating, compressor operation, and heat treatment phases.
While the incorporation of clean, renewable energy sources can reduce carbon emissions, challenges like power supply limitations, unit costs, and equipment investments exist. Government subsidies and other support measures can play a crucial role in expediting the transition toward electrification.
In light of climate change and resource conservation efforts, recycling and reuse of vehicles has gained importance. Even in Europe, where environmental awareness is high, many older vehicles are exported to secondary or tertiary countries, resulting in insufficient recycling. Cars include diverse materials such as metal, glass, plastic, electric products, and electronic components, and each material requires different methods of recycling. Among them, steel has the highest recycling rate, while composite materials containing metal and plastic still pose a challenge as some plastics cannot be effectively recycled.
The primary challenge of recycling EVs is in the battery system. EV components include high value critical metals (such as cobalt, nickel, manganese, and lithium) and large structural materials (such as steel and plastic). Complete recycling and reuse of EVs is still not possible under current recycling technology. As such, many automakers are actively working on battery recycling. Current progress includes demonstration plants, research and development, and patent filings.
For example, Mercedes-Benz has partnered with a carbon conversion company to convert carbon dioxide to raw materials for products or fuel used to manufacture components.
As global automakers accelerate towards carbon neutrality, they have begun to demand downstream suppliers implement energy saving and improvement plans to decrease carbon dioxide emissions. These plans include energy conversion, energy saving in manufacturing processes, recycling, and green materials.
Four trends have been observed in the automotive industry in the move towards carbon neutrality: (1) Global benchmark automakers are striving to mass produce EVs to accelerate universal adoption; (2) Vehicle production requires the use of extensive steel, but several challenges are impeding the use of green steel; (3) Vehicle and component suppliers continue to promote green factories and energy management systems, implement green manufacturing processes, promote advanced manufacturing processes and digital transformation, and optimize production; (4) The automotive industry continues to build circular systems for recycling and reuse of critical materials by recycling and re-manufacturing components.
Source: Metal Industries Research & Development Centre Metal Industry Intelligence