- The next website linking is only available in Chinese.
- If you have any questions, please dial +886-2-2311-2031.
Continue to the website.
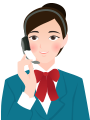
2023-12-26
The COVID-19 pandemic ravaged the global airline industry and resulted in US$201 billion in cumulative losses for the airline industry from 2020 to 2022. To expedite recovery from the impacts of the pandemic, countries and aviation industry supply chains across the world are actively seeking new development strategies and adopting net zero carbon emission goals as a means to revitalize the aviation manufacturing industry. The global aviation industry has pledged to attain net zero emissions by 2050, which in turn drives major international aerospace manufacturers to adopt alternative energy sources (e.g., sustainable aviation fuel (SAF), hydrogen, and electricity) for propulsion system and engine development. It also gives rise to technical challenges, as well as business opportunities, for the engine industry and related component manufacturers.
In recent years, the supply chains of the aviation industry in many countries have embraced carbon reduction. This is due to the fact that Western countries and competitors are setting carbon reduction targets ahead of schedule, which is accelerating the development of carbon reduction technologies in the aviation supply chain. According to the International Air Transport Association (IATA), the global aviation industry is committed to attaining its net zero carbon emission objectives by 2050 through the following means: (1) Increasing the use of sustainable aviation fuel (SAF) ; (2) Adopting new electric power and hydrogen technologies; (3) Increasing the operating efficiency of aviation infrastructure and air traffic management; (4) Using technologies such as carbon offsetting or carbon capture.
In response to carbon reduction trends in the aviation industry, major aircraft and engine manufacturers such as Airbus, Boeing, GE Aerospace, and Safran have announced development plans for new energy aircrafts or unveiled plans for test flights and commercial operation of concept aircrafts.
In September 2020, Airbus unveiled three zero-emission concept aircrafts dubbed “ZEROe”. All three aircrafts use liquid hydrogen as primary fuel and are equipped with hybrid hydrogen-electric fuel cells in the propulsion system. Airbus expects hydrogen fuel propulsion technology to be fully developed by 2025 and plans to bring three types of hydrogen-powered commercial aircrafts to market by 2035.
Boeing mainly implements carbon reduction measures and assists downstream customers in carbon reduction through the following: (1) Continuous development of more efficient aircrafts; (2) Investment, development, and use of SAF; (3) Improve eco-friendly operations of Boeing plants, work sites, and supply chains; (4) Assist customers in improving fleet efficiency.
SAF technologies adopted by Boeing incur a lower technical barrier than the development of hydrogen propulsion systems. Boeing will therefore prioritize the use of SAF and airworthiness tests. In early 2021, Boeing pledged that all aircrafts produced by Boeing will be capable and certified to fly on 100% SAF by 2030. In 2022, Boeing announced a supply agreement with EPIC Fuels, which will provide 2 million gallons of SAF for commercial aircraft operations and marks the largest SAF purchase in history. Boeing regards SAF as the most direct means for decarbonization in the aviation industry and plans to use SAF to reduce costs.
On June 14, 2021, GE Aerospace and Safran announced the extension of their joint venture partnership in CFM International to 2050, as well as the launch of the Revolutionary Innovation for Sustainable Engines (RISE) program to develop new engines that will cut fuel consumption and carbon emissions by more than 20%. The new engine program encompasses fan architecture and compatibility with alternative energy sources, and is expected to begin commercial operations in the mid-2030s. It will increase the fuel efficiency of narrow-body aircrafts and reduce carbon emissions.
Domestic aviation component manufacturers have become key players in the international aerospace industry chain, and they form a critical supply chain of fuselage structural components, composite materials, and fan blades for many major foreign manufacturers. Major manufacturers must still overcome several technical challenges in the development of aircrafts powered by alternative energy, such as the 100% SAF airworthiness test, battery capacity, range, weight, charging issues, challenges posed by hydrogen storage and hydrogen incineration systems on the fuselage, engine architecture, component design, and material usage, and the certification of new technologies and new materials. Nevertheless, the outlook for development of new aircrafts and new engines remains positive, and future development and technological advancements continue to hold promise.
The domestic industry is constrained by the typical characteristics of the aviation industry, which include requiring the original manufacturer’s certification of materials, personnel, and processes, as well as high capital investment and certification costs, which creates difficulties when attempting to make adjustments to the industry. In addition, the domestic engine supply chain consists mainly of Tier-1 suppliers of entire machines, such as Aviation Industry Development Company (AIDC), which forms cooperative and subcontracting networks. Only a handful of manufacturers directly supply major foreign companies, which makes it difficult for Taiwanese companies to participate in the risk-and-return-sharing mechanisms of major foreign manufacturers or access the development and design of new components. Therefore, companies can only remain passive and wait for product specifications and purchase orders from downstream customers, as they are unable to participate in R&D, business opportunities in new markets, and/or new products created by carbon reduction trends.
Nevertheless, major manufacturers regard carbon emission management along the supply chain as a carbon reduction strategy. They are also changing production sites or continuously cutting prices to reduce production costs in recent years. As such, carbon emissions will become a critical factor in production costs and supply chain management in the foreseeable future. The effects are particularly prominent in development trends and markets for engine technology. The RISE program with CFM International is expected to give rise to a new wave of replacements in the next ten years. To meet the requirements for alternative energy, new engines will be different in many aspects, i.e., the use of lightweight materials and the structural design of components. Korea and other competitors are actively improving technologies such as smart and additive manufacturing for aerospace to increase productivity and ramp up production capacity for lightweight and integrated components. Therefore, Taiwanese suppliers must identify new digital technology applications or processing technologies, increasing the performance and efficiency of the production process, processing method, and the management of plants and personnel to directly or indirectly reduce emissions and increase competitiveness.
Source: Metal Industries Research and Development Centre Metal Industry Intelligence