- The next website linking is only available in Chinese.
- If you have any questions, please dial +886-2-2311-2031.
Continue to the website.
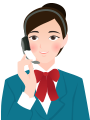
2024-06-17
MOEA, Infineon jointly announce new R&D center in Taiwan
MOEA Minister Kuo Jyh-huei (from right), German Institute Taipei Director-General Jörg Polster and Sam Geha, Infineon head of ICW business, are all smiles during a press event announcing a new Infineon R&D center June 17 in Taipei City. (Courtesy of MOEA) Germany-based automotive semiconductor heavyweight Infineon Technologies AG will set up a new research and development facility in Taiwan, reflecting the country’s growing prominence in the automotive chip sector, the Ministry of Economic Affairs said June 17. According to the MOEA, the Infineon Advanced Automotive and Wireless Communication Semiconductor R&D Center will be the first of its kind by a European chip manufacturer in Taiwan and is expected to help establish the country as a major automotive chip development hub. In a news conference in Taipei City, MOEA Minister Kuo Jyh-huei said Taiwan plays a critical role in the global semiconductor manufacturing supply chain and is a leader in information and communication technologies applications. The facility will help introduce advanced automotive wireless control technology to the country, promote cooperation with international counterparts and expand local firms’ presence around the world, he added. Echoing Kuo’s remarks, Sam Geha, head of internet of things, compute and wireless business at Infineon, said that after operating 25 years in Taiwan, the company is deeply impressed by Taiwan’s vibrant entrepreneurial ecosystem, including its top-notch R&D talent pool and strong industry clusters. Building on Infineon’s existing wireless research lab in Taiwan and with support from the MOEA, the new center will work with the firm’s local partners to jointly develop innovative ICs and solutions for the automotive sector, he said. The MOEA expects the new center to spur investment totaling NT$2.7 billion (US$83.37 million) and create output estimated at NT$60 billion for Taiwan’s electric vehicle sector. (SFC-E)
2023-09-28
Analysis of the Strategic Activities of Benchmark Electric Vehicle Manufacturers Under the Trend of Carbon Neutrality
Introduction Carbon emissions are mostly generated during the “driving stage” of the life cycle assessment (LCA) of vehicles. As such, the primary trend is reducing fuel consumption and transitioning towards electric or hydrogen energy. Therefore, this article will explore the 4 major strategies of major global manufacturers: electrification technology, adopting eco-friendly materials, energy transitioning for manufacturing faciities, and circular recycling. I. Electric Vehicle Technology The top global automakers are actively expanding their lineup of electric vehicles. Amongst European automakers, the EU has pledged to achieve carbon neutrality by 2050 and ban sales of fuel vehicles in 2035. German automakers such as VW, Audi, BMW, and Mercedes-Benz have all responded positively to this policy. LCA reveals that batteries are the key to decreasing the carbon emissions of a whole vehicle. The source of electricity for charging batteries, as well as the manufacturing technology, will affect the overall emissions of the vehicle throughout LCA. Within the automotive sector, numerous automakers are proactively advancing the research and implementation of fuel cell systems for/towards decarbonization and bolstering energy security, as exemplified in the following cases: Toyota released their first fuel cell vehicle, MIRAI, as early as 2014. But the lack of infrastructure (such as hydrogen stations) saw global sales of a mere 10,000 vehicles. Honda and GM co-developed next-gen fuel cell systems that strive to enhance performance, decrease costs, and extend lifespan. European automakers such as Stellantis and BMW have also accelerated production of fuel cell vehicles, making an active contribution towards carbon neutrality. In response to environmental challenges, they are also furnishing hydrogen-based transportation in the future. II. Adopting Eco-friendly Materials Steel production, a major part of vehicle manufacturing, is one of the main sources of carbon dioxide emissions. All major global steel companies are actively seeking solutions to this problem. By substituting with hydrogen, there is a global effort to achieve an eco-friendly steel production process. The following are some examples: Mercedes-Benz has pledged to achieve carbon neutrality in the production process and supply chains of newly manufactured vehicles by 2029 at the latest. Along with Swedish steel company SSAB and French automotive component supplier Faurecia, Benz signed an agreement for utilizing eco-friendly steel in the exterior body plating of vehicles, as well as in seats. In contrast, VW has adopted multiple strategies including the recycling of internal aluminum scraps, broken glass, and waste plastics to promote recycling and reuse. BMW has partnered with Emirates Global Aluminium to utilize aluminum materials produced with green energy. BMW is also working with Salzgitter AG to provide low carbon steel. The plan is to increase the proportion of recycled steel materials to 50% by 2030. However, the promotion of green steel is currently facing three major challenges. The industry needs a sufficient supply of renewable energy and green hydrogen, as well as enough waste steel. The third challenge is that current technologies still need to catch up, such as direct reduction hydrogen - electric furnace technology. The industry and governments need to work together to promote production and application of eco-friendly steel. Ⅲ. Energy Transitioning for Manufacturing Facilities Although the initial expenses of adopting advanced manufacturing equipment in factories can be substantial, these investments have resulted in substantial energy savings as the car manufacturing industry undergoes its digital transformation. For example, Japanese company Omron provides smart factory diagnosis services to visualize data like carbon dioxide emissions, electricity, energy consumption, and output. On the other hand, major German automakers use renewable energy to meet energy saving targets. VW factories are generating their own solar energy, while Mercedes-Benz has partnered with German energy suppliers to purchase solar, wind, and hydro energy. Casting and aluminum alloy die-casting generate the highest amount of carbon emissions in the manufacturing process due to the substantial heat energy required. In casting, energy consumption rises during material heating, compressor operation, and heat treatment phases. While the incorporation of clean, renewable energy sources can reduce carbon emissions, challenges like power supply limitations, unit costs, and equipment investments exist. Government subsidies and other support measures can play a crucial role in expediting the transition toward electrification. Ⅳ. Recycling and Circular Production In light of climate change and resource conservation efforts, recycling and reuse of vehicles has gained importance. Even in Europe, where environmental awareness is high, many older vehicles are exported to secondary or tertiary countries, resulting in insufficient recycling. Cars include diverse materials such as metal, glass, plastic, electric products, and electronic components, and each material requires different methods of recycling. Among them, steel has the highest recycling rate, while composite materials containing metal and plastic still pose a challenge as some plastics cannot be effectively recycled. The primary challenge of recycling EVs is in the battery system. EV components include high value critical metals (such as cobalt, nickel, manganese, and lithium) and large structural materials (such as steel and plastic). Complete recycling and reuse of EVs is still not possible under current recycling technology. As such, many automakers are actively working on battery recycling. Current progress includes demonstration plants, research and development, and patent filings. For example, Mercedes-Benz has partnered with a carbon conversion company to convert carbon dioxide to raw materials for products or fuel used to manufacture components. Ⅴ. Conclusion As global automakers accelerate towards carbon neutrality, they have begun to demand downstream suppliers implement energy saving and improvement plans to decrease carbon dioxide emissions. These plans include energy conversion, energy saving in manufacturing processes, recycling, and green materials. Four trends have been observed in the automotive industry in the move towards carbon neutrality: (1) Global benchmark automakers are striving to mass produce EVs to accelerate universal adoption; (2) Vehicle production requires the use of extensive steel, but several challenges are impeding the use of green steel; (3) Vehicle and component suppliers continue to promote green factories and energy management systems, implement green manufacturing processes, promote advanced manufacturing processes and digital transformation, and optimize production; (4) The automotive industry continues to build circular systems for recycling and reuse of critical materials by recycling and re-manufacturing components.
2023-06-30
Automotive Semiconductors Attract Investments at the 2023 Online Industry Investment and Business Opportunities Exchange for the European Region
Taiwan, as a global leader in semiconductors, has become an important partner to major international high-end chip and semiconductor brands. Applications for automotive semiconductors (i.e., automotive electronics, vehicle safety, mobile assistance, communication multimedia, and automotive ICs, etc.) has also been established as a niche field in Taiwan. Our manufacturing capabilities are also trusted by major global automotive companies. According to statistics, domestic output value of automotive electronics was approximately NT$355 billion in 2022-a number that is projected to grow to NT$600 billion in 2025, with a high compound annual growth rate of 14%, due to the continuous development of smart and autonomous driving technology. To enhance investment cooperation between foreign businesses and domestic industries, the Department of Investment Services of the MOEA, held the 2023 Online Industry Investment and Business Opportunities Exchange for the European Region on June 29. By partnering with overseas diplomatic missions and economic divisions in the UK, the Netherlands, Denmark, Switzerland, Italy, Germany, Frankfurt, France, Spain, and Sweden, the DOIS invited major global companies like Volvo, Valeo, and FCA Italy to join in online, and took the opportunity to share the investment environment, capacities, and opportunities within Taiwan`s automobile semiconductors. InvesTaiwan CEO Emile M. P. Chang, in his opening remarks, stated that Taiwan maintains its key role and position with global industries, despite many worldwide economic impacts such as US and China trade conflicts, global inflation, Russian invasion of Ukraine, etc. As such, he invited European businesses to invest in Taiwan and enter global markets together. SEMI Senior Director Jo-Ann Su, shared development trends in the global and Taiwan semiconductor industries and pointed out that in recent years, international enterprises have been working closely with Taiwan companies to promote the growth of the automobile semiconductor industry-recognition from global automobile brands for the technology and innovation of Taiwan`s semiconductor industries. Jason Huang, President of Sentec-Taiwan`s leading integrated manufacturer of automotive and motorcycle electromechanical systems-discussed applications of compound semiconductors in next-generation vehicles. He also explained the structure of the global supply chain for EV power modules, as well as advantages and investment opportunities of Taiwan`s industrial chain. Through the event, DOIS gained a better understanding of the investment needs of foreign businesses, conveyed Taiwan`s investment environment, and enhanced the inclination to invest in Taiwan. A US session is slated for August and shall focus on opportunities for collaboration in satellite communication ground equipment, aiming to encourage foreign businesses to invest in Taiwan. Spokesperson:Li Min-Hsi, Deputy Director General, DOIS Tel.:02-2389-2111 ext. 812, 0966-118-638 E-mail:mhlee@moea.gov.tw Contact:Ms. Chen Ying-Ju, Section Chief, DOIS Tel.:02-23892111 ext. 210 E-mail:yjchen2@moea.gov.tw
Complete automotive industry supply chain
Suitable testing environment for self-driving vehicle
Extensive experience with information security technologies
Autonomous vehicles
The government is using advanced driver assistance systems (ADAS) as the basis for legislative amendments designed to improve traffic safety.
Self-driving vehicles
Legal basis: Taiwan's national legislature in 2018 passed the "Unmanned Vehicles Technology Innovative Experimentation Act." Drawing upon the "regulatory sandbox" spirit, this act provides a statutory basis for loosely regulated experimental efforts to develop new types of unmanned vehicle technologies.
Testing sites: They include the Taiwan CAR Lab in Shalun, Tainan for testing vehicles such as mid-sized buses or smaller. Hutoushan Innovation Hub in Taoyuan City uses the Internet of Vehicles (IoV) & Smart Driving Center and Information Security IoT Center to test autonomous vehicles under a wide variety of simulated environments.
In November 2019, Sumitomo Corporation invested in RAC Electric Vehicles, spending NT$126 million to obtain a 7% equity stake. Sumitomo will rely on RAC to perform electric bus manufacturing and related services, while RAC will rely on Sumitomo's marketing and services network to expand its international markets.
NVIDIA, a US maker of graphics chips, has signed a letter of intent to engage in cooperation with the National Applied Research Laboratories (NARLabs), which is subordinate to Taiwan's Ministry of Science and Technology. NVIDIA will take part in efforts to develop Taiwan's autonomous vehicle industry, and will cooperate with Taiwan CAR Lab on technology applications. In addition, Canadian auto parts maker Magna, has already had an R&D center in Taiwan for several years where the company has been working to develop ultrasonic sensors, parking/reverse assist systems, automotive imaging, and forward camera modules and systems. And now Magna is drawing up plans for an additional investment to engage in further R&D work on new technologies.
The Volkswagen Group Taiwan Training Academy that was established in Xizhi District of New Taipei City is Volkswagen's biggest training institution anywhere in Asia outside of mainland China. Recently, in order to embark upon Taiwan's electric vehicle market, Volkswagen established the "e-Mobility Center" to train professionals with special expertise in maintenance of Taiwan-made electric vehicles, and to engage in cooperation with Delta Electronics, Inc. on the development of EV charging infrastructure. In addition, Honda Taiwan is cooperating with technical and vocational schools in Pingtung County to train technicians and provide young graduates with employment opportunities.
Source: InvesTaiwan
Email:service@invest.org.tw / Information Window for Key Innovative Industries
Add: 1F., No. 82, Aiguo E. Rd., Zhongzheng Dist., Taipei City 100031 , Taiwan(R.O.C)
Download
Key Innovative Industries in Taiwan - Next-Generation Vehicle (12.0 MB)